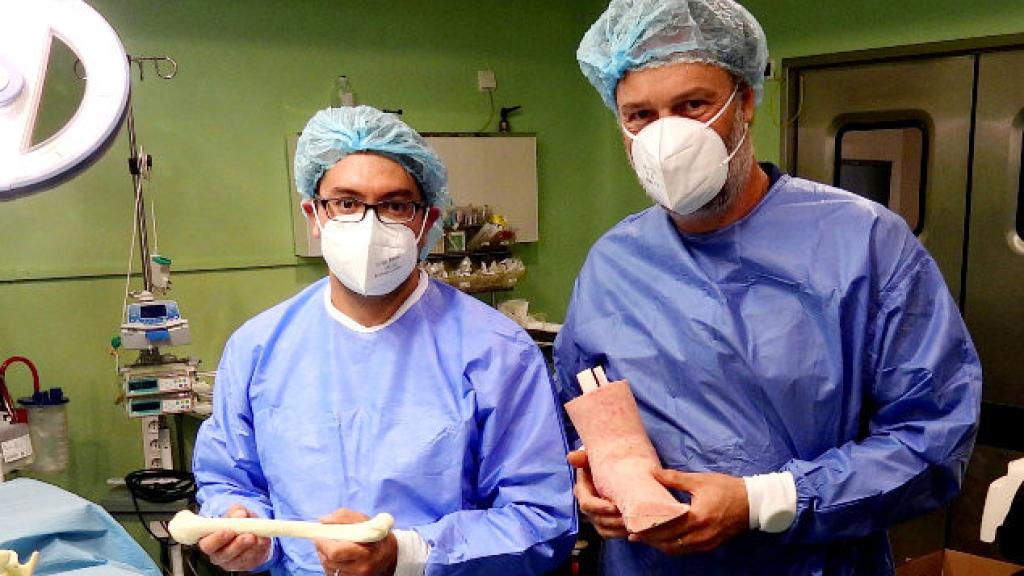
Pedro Enrique Martínez González, técnico universitario en Anatomía, y José Antonio Acosta Martínez, doctor en Ciencias de la Salud, mostrando un par de biomodelos que producen en su startup Arthromodel.
Los cirujanos cambian cadáveres por las manos y los pies de estos murcianos para ensayar con el bisturí
Johnson & Johnson es uno de las clientes de Arthromodel: una startup pionera por su producción de réplicas anatómicas en el CEEIM de Murcia.
20 marzo, 2023 03:03Podría calificarse como de alto secreto casi todo lo que se 'cuece' dentro del espacio que tiene habilitado Arthromodel en el Centro Europeo de Empresas e Innovación de Murcia. La privacidad es una de las máximas que rige el trabajo de esta startup dedicada a fabricar biomodelos: replicas exactas de 'carne' y 'hueso' de la anatomía humana, que permiten a cirujanos, traumatólogos o podólogos ensayar nuevas técnicas de abordaje quirúrgico, antes de aplicarlas a pacientes reales sobre la mesa de operaciones.
La actividad de Arthromodel es pionera en nuestro país: sus biomodelos personalizados de pies, manos, tobillos, incluso de la columna vertebral, son la alternativa a la tradicional pieza cadavérica que usan los médicos para entrenarse con el bisturí.
La adquisición de un cadáver cuesta unos 2.000 euros, exige mucha burocracia y solo se puede utilizar en una Facultad de Medicina, en un Instituto Anatómico Forense o en un hospital con sala de tanatopraxia, mientras que el coste de estas réplicas de la anatomía del paciente que produce esta empresa, oscila de 150 a 400 euros. Además, se pueden usar en cualquier espacio porque no tienen actividad enzimática ni microbiológica, y se desechan una vez culminada la práctica quirúrgica.
"En España no hay ninguna empresa que los fabrique: somos la única que hace réplicas de todas las regiones del cuerpo humano", tal y como subraya con mucho orgullo Pedro Enrique Martínez González (Murcia, 1985), técnico universitario en Anatomía, y uno de los dos socios fundadores de Arthromodel. "Este campo está bastante virgen, hay demanda y esa demanda está mal cubierta", según corrobora José Antonio Acosta Martínez (Murcia, 1970), doctor en Ciencias de la Salud y la otra mitad del corazón de esta novedosa startup con sello murciano.
Arthromodel, la startup dedicada a fabricar biomodelos
Casi nadie accede a la sede de Arthromodel en el CEEIM: un pequeño Silicon Valley, en el Campus de Espinardo de la Universidad de Murcia, donde se incentiva la creación de empresas innovadoras y de base tecnológica. De sus instalaciones, sus socios solo cuentan que albergan ordenadores, impresoras 3D, tornos, fresadoras de control numérico, sierras especiales, así como productos químicos para desarrollar los huesos y tejidos de sus biomodelos de extremidades superiores e inferiores que incluyen músculos, ligamentos, tendones, nervios, líquido sinovial, venas, sangre…
"Nuestro sector tiene un componente de innovación que muchas veces es secreto industrial", tal y como advierte, el biólogo y doctor en Ciencias de la Salud, José Antonio Acosta Martínez. En la producción de un biomodelo personalizado pueden llegar a invertir meses de trabajo, ya que su grado de realismo es vital para lograr que los cirujanos simulen con mayor seguridad una operación. Todo ello, para lograr varios objetivos en el quirófano: ejecutar la intervención en el menor tiempo posible, con menos errores y con periodos más cortos de recuperación para el paciente.
El nicho de mercado de esta empresa es enorme: desde fabricantes de instrumental médico; a distribuidoras que producen material quirúrgico y necesitan hacer ensayos con placas, tornillos y clavos intraóseos; sociedades médicas que organizan jornadas sobre cirugía mínimamente invasiva, incluso facultades de Medicina, Enfermería y Podología de todo el país.
Tal es el nivel de realismo y fidelidad morfológica de los biomodelos de Arthromodel que uno de sus clientes es la norteamericana Johnson & Johnson: fabricante de dispositivos médicos y productos farmacéuticos, presente en más de sesenta países, y que ocupa el sexto puesto a nivel mundial en productos biológicos y el quinto en el ámbito farmacéutico.
Un biomodelo de Arthromodel consistente en un tobillo con equimosis y fractura en el maleolo tibial.
- ¿Cómo surge la idea de montar una startup dedicada a producir modelos sintéticos que buscan replicar la anatomía del paciente?
- Pedro Enrique Martínez: Yo antes era técnico de anatomía humana y detecté que en los cursos de formación de las facultades de Medicina había una necesidad, en el sentido de que siempre se tenía que tirar del cadáver para hacer una formación más especializada y observé que en el mercado nacional no había este tipo de actividad profesional. Es decir, no existía ninguna empresa que pudiera suministrar material para abordajes quirúrgicos, entrenamientos en cirugía ortopédica y traumatológica, formación de enfermeros, podólogos…
No había ninguna empresa que fabricase biomodelos y a nivel mundial solo estaba la de Shawn Bones, en la costa oeste de Estados Unidos. Y poco más. No sé si hay una empresa también en Suiza, pero tiene la fabricación en Asia.
Corría el año 2018, cuando en el camino de este técnico de anatomía se cruzó el biólogo, José Antonio Acosta Martínez, enfrascado en una importante tesis doctoral sobre biomateriales y medicina regenerativa. De aquella amistad en la que no faltaban conversaciones sobre sus respectivos sectores profesionales, surgió la idea de crear una empresa dedicada a producir réplicas de la estructura anatómica humana.
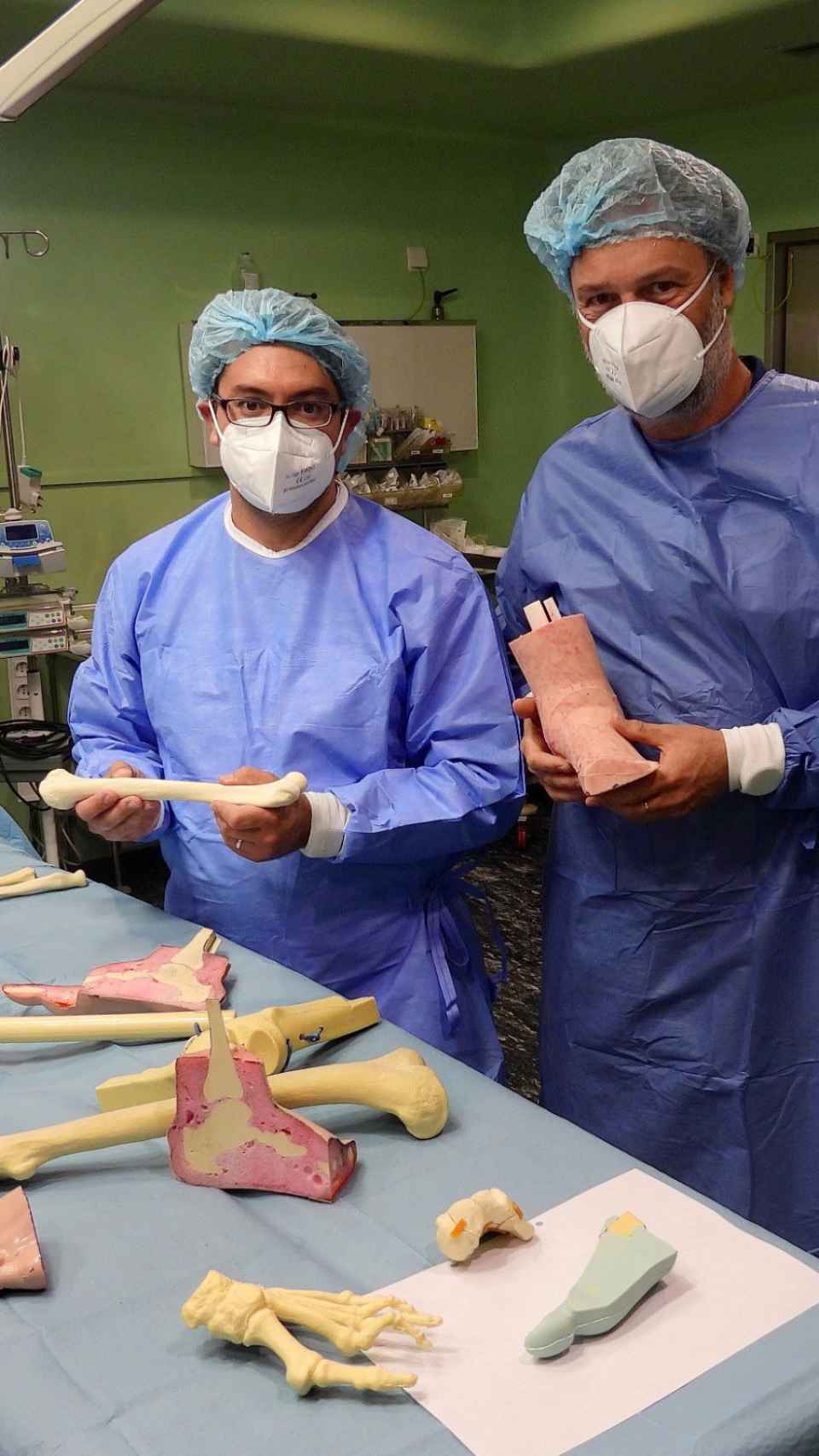
Pedro Enrique Martínez González, técnico universitario en Anatomía, y José Antonio Acosta Martínez, doctor en Ciencias de la Salud, son los socios fundadores de Arthromodel.
"Es un proyecto de garaje, como se suele decir en Estados Unidos, de muchas pruebas de ensayo-error, probando con materiales, combinándolos y analizando sus propiedades mecánicas", según resume José Antonio, un crack autodidacta de la impresión 3D y del diseño de ordenador que se ocupa de la parte de innovación de esta empresa. Por su parte, Pedro Enrique aporta sus conocimientos en anatomía y los contactos con empresas y médicos para establecer una red de hasta cuarenta clientes en España. Lograrlo no ha sido fácil porque tuvieron que realizar pruebas durante más de un año.
"Estuvimos haciendo ensayos hasta que dimos con un material que era igual que el que se importaba de Estados Unidos", recuerda José Antonio. "Y constituimos la empresa una semana antes de que estallase la pandemia de coronavirus". De forma que les tocó afrontar una larga travesía por el desierto, sin poder explotar comercialmente sus biomodelos y sus réplicas de hueso sintético y de anatomía del esqueleto.
"Mantuvimos una actividad de subsistencia, muy orientada al desarrollo y a la innovación", según resume el cerebro I+D de esta startup. Tras concluir el confinamiento, se produjo el despegue de Arthromodel, en un episodio donde una publicación en redes sociales se convirtió en el mejor escaparate para sus biomodelos: "Johnson & Johnson se fijó en nosotros porque colgamos en Linkedin, un prototipo de un modelo de esqueleto de pie, con patologías, recubierto de carne, era algo muy preliminar, pero de la noche a la mañana nos involucraron con ellos en un proyecto muy chulo".
El resultado de ese encargo de la multinacional norteamericana fue un biomodelo que reproducía un tobillo, con fracturas complejas de tibia y peroné, con los huesos encapsulados en un símil de tejidos blandos: piel, médula ósea, sangre y líquido sinovial.
- ¿Cómo reproducen las lesiones en sus biomodelos para que los médicos puedan ensayar técnicas de abordaje?
- José Antonio Acosta Martínez: Trabajamos con imagen médica. El cliente nos proporciona el escáner de un paciente con fracturas de tobillo y nosotros hacemos una representación tridimensional, a escala real, en una pieza en la que se pueden desarrollar experiencias [quirúrgicas] y actos de aprendizaje [médicos] que no se pueden realizar con un cadáver. Un biomodelo nunca será comparable a una pieza natural, pero sí que es verdad que trabajando con un escáner podemos hacer réplicas de casos clínicos concretos para practicar técnicas que luego utilizarán en una operación.
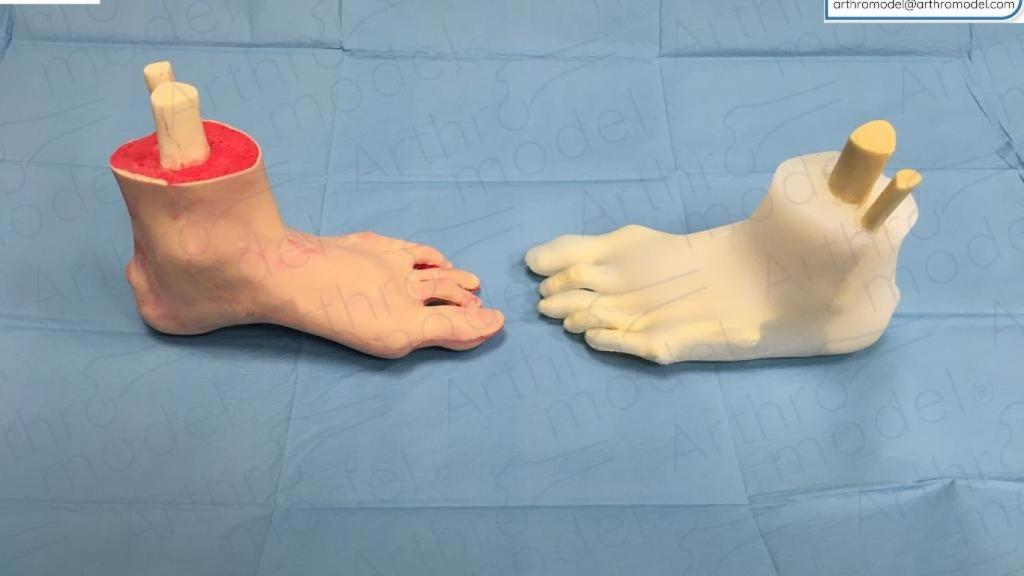
Los biomodelos de pies que incluyen un tobillo fracturado son uno de los pedidos más recurrentes que recibe esta compañía, por parte de traumatólogos.
- Dentro del secreto industrial que rige la actividad de su empresa, ¿me puede contar algo sobre los materiales que emplean para lograr el realismo que tienen sus biomodelos?
- Eso no se lo puedo decir: el último material lo probamos este miércoles. Nosotros estamos todo el tiempo probando materiales nuevos. Ahora estamos tratando de producir cartílago, con materias primas de distintos sectores, para que le guste al médico y cuando meta el bisturí simule un tacto parecido. Estamos empleando siliconas, espumas, polímeros, elastómeros, resinas, colorantes, acelerantes, espesantes… Por ejemplo, para emular la musculatura usamos espuma flexible y geles.
En nuestro taller tenemos docenas y docenas de productos químicos diferentes y empleamos desde técnicas clásicas de moldeo, a modelado por ordenador, tecnología 3D para la impresión con resinas, fotogrametría, captación de imagen, escaneado 3D… En cuanto a los huesos que reproducimos, normalmente, están impresos en un material que permite a los médicos taladrarlos, colocarles algún tornillo o una placa.
La innovación en sus procesos es continua para replicar al milímetro la textura, forma, dimensiones y posición de cualquier pieza de la anatomía humana. El grado de exigencia autoimpuesto en el diseño de modelos anatómicos sintéticos y huesos elaborados con resinas mecanizables, le ha permitido a Arthromodel reproducir casos clínicos específicos -de pacientes reales- que facilitan a los cirujanos una experiencia formativa que no podrían desarrollar con piezas cadavéricas naturales.
Además, al ser artificiales sus biomodelos, presentan menores limitaciones sanitarias, asociadas a su manipulación, exigen menores trámites administrativos y un coste más económico que una pieza cadavérica. Tales circunstancias han permitido a esta startup incorporar a su cartera de clientes a otras dos empresas internacionales: Stryker y Smith & Nephew.
- ¿Cuáles son las réplicas que más les demandan desde las distribuidoras de instrumental quirúrgico y sociedades médicas?
- Pedro Enrique y José Antonio: El biomodelo de tobillo polifracturado porque fue muy notorio. También nos piden muchas piezas de pie y manos con encapsulado flexible. Todos ellos son modelos complejos, el tope de nuestra gama, porque llevan fracturas diseñadas en impresión 3D mecanizada, que permite cortar y fresar esas fracturas, además de colocarle placas, tornillos... Esas fracturas son reproducciones de escáner y TAC médicos, de un paciente real, que nos facilita el cliente, a las que luego aplicamos una textura.
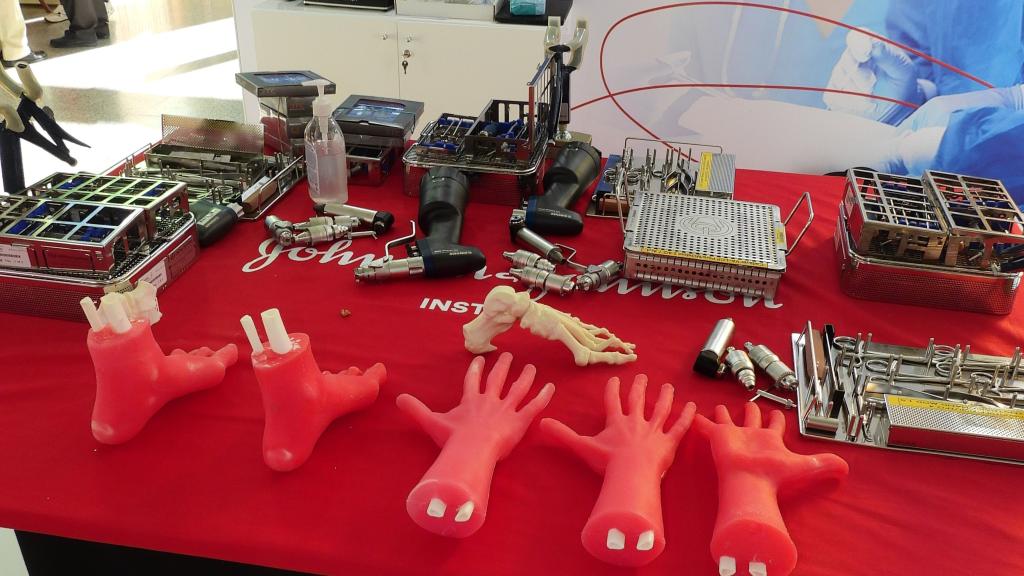
Las réplicas sintéticas de pies y manos son los mayores pedidos que recibe Arthromodel.
- ¿Hay alguna zona de la anatomía que ustedes no sean capaces de replicar artificialmente?
- Pedro Enrique Martínez: Al haber estado en las salas de disección, conozco las densidades de los huesos y su morfología. Producimos desde extremidades superiores a inferiores. También podemos replicar un hematoma o un símil de la sangre, con el mismo aspecto y densidad. Ahora acabamos de sacar la línea de columna vertebral y también estamos trabajando con médicos de Traumatología Infantil, las malformaciones congénitas que sufren los niños durante el desarrollo embrionario.
Estos profesionales no tienen forma de practicar una intervención quirúrgica en casos así de concretos, donde los niños no pueden caminar porque no desarrollan bien sus huesos del pie, de la tibia o de la rodilla. Esos médicos no pueden trabajar con piezas cadavéricas, para ensayar sus técnicas, para enderezar huesos o colocar fijadores externos a niños, debido a que está prohibido usar el cadáver de un menor. De modo que estamos colaborando con ellos, desarrollando biomodelos de osteogénesis imperfecta, de los TAC que nos facilitan de Traumatología Infantil.
Prácticamente, se podría decir que solo se nos escapa reconstruir una cara, por la complicación que conlleva, aunque a nivel de trauma sí que hacemos reproducciones de las mandíbulas y de los senos maxilares.
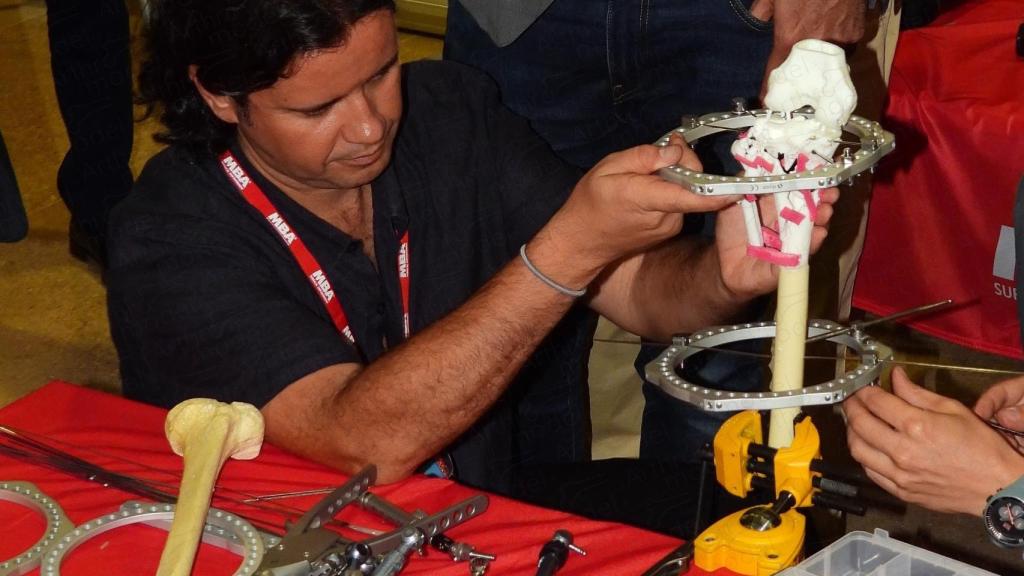
El doctor César Salcedo, especialista en Cirugía Ortopédica y Traumatología Infantil del Hospital Virgen de la Arrixaca de Murcia, colocando un fijador externo en una réplica del hueso de un niño.
No hablan en vano los socios fundadores de Arthromodel: su empresa es la principal productora nacional de réplicas anatómicas. Le han fabricado biomodelos a alumnos de Enfermería para que ensayen la punción intraósea, para extraer líquido medular; a una empresa le hicieron modelos de rodilla, con una densidad específica de hueso y que no articulase bien, con el objetivo de probar sus prótesis antes de lanzarlas al mercado; a la Sociedad Española de Cirugía Ortopédica y Traumatología le diseñaron pies y manos para su congreso anual, donde médicos residentes practicaron reducciones de fractura de radio o de calcáneo en el talón...
Básicamente, se puede afirmar que no les falta trabajo porque esta empresa ha buscado soluciones a necesidades más complejas del sector médico, al margen de limitarse a producir piezas de hueso sintético. Cosa que también hacen y a gogó. "Los producimos por docenas y tardamos minutos porque se fabrican con un molde", según aclara el biólogo José Antonio Acosta. Unas veces los diseñan con impresión 3D y otras de forma tradicional, combinando productos como la espuma líquida.
"El coste de los huesos oscila de 8 a 25 euros, aunque el precio varía en base a si es hueso solo o combinado con articulaciones: no cuesta lo mismo una rodilla que un fémur con tibia y peroné", tal y como ejemplifica José Antonio Acosta. "Producimos huesos sanos y patológicos, solo recurrimos al 3D cuando el encargo tiene muchas malformaciones, aunque lo que más se consume es el hueso clásico al que le hacemos unas fracturas para que los traumatólogos puedan reducirlas con placas, tornillos o fijadores externos", según agrega su socio, Pedro Enrique Martínez.
- ¿En la réplica de qué biomodelo andan enfrascados ahora mismo?
- Pedro Enrique y José Antonio: A veces, no es tanto las piezas que nos faltan por replicar, sino técnicas con las que nuestros modelos sean operativos. Nuestros productos son viables con rayos 'X', pero con el tema de la ecografía estamos analizando su compatibilidad para ajustar las propiedades de nuestras piezas a técnicas quirúrgicas, como la artroscopia de rodilla. Nuestro objetivo siempre es innovar con nuevos productos para adaptarnos a un mercado en continuo desarrollo como la medicina.