Un grupo de mujeres con bata blanca y el pelo recogido separa una montaña de dientes bajo el cálido haz de luz de un foco. Con precisión milimétrica, seleccionan las piezas según su forma y las colocan en una larga caja de madera con distribuidores que, después, otra persona se encarga de revisar y reorganizar. José Domínguez supervisa todo el proceso mientras camina entre las decenas de máquinas, robots y cintas que rodean a las artesanas y que distribuyen, en procesión mecánica, los miles de colmillos y muelas que después irán a parar a las bocas de millones de pacientes de clínicas dentales de todo el mundo.
Domínguez es el director general de esta fábrica, bautizada como Unidesa-Odi, acrónimo de 'Unión Dental de Ortodent Dental Industrias'. A su lado tiene a su hijo Guillermo, subdirector general de la empresa; a su hermana Soraya, directora de exportaciones y presidenta del consejo, y al hijo de esta, Sergio Tekogul, responsable de marketing. Además, sobre todos ellos sobrevuela la supervisión –en calidad de jubilada– de su madre, Ana María Álvarez, de 95 años, matriarca de los Domínguez y espíritu incombustible del negocio, ya que fue ella quien se quedó al frente de la industria cuando el verdadero fundador, su marido José, falleció hace cuatro décadas.
Hoy los hijos de José y Ana María están al frente de este taller, el único de España dedicado a la fabricación de dientes artificiales y discos para ortodoncias y prótesis dentales. Un negocio que, como todas las grandes compañías que después han sido únicas en su especie, nació en un pequeño garaje, concretamente en 1952, en León. Media centuria después, su centro de operaciones está radicado en la madrileña localidad de Tielmes.
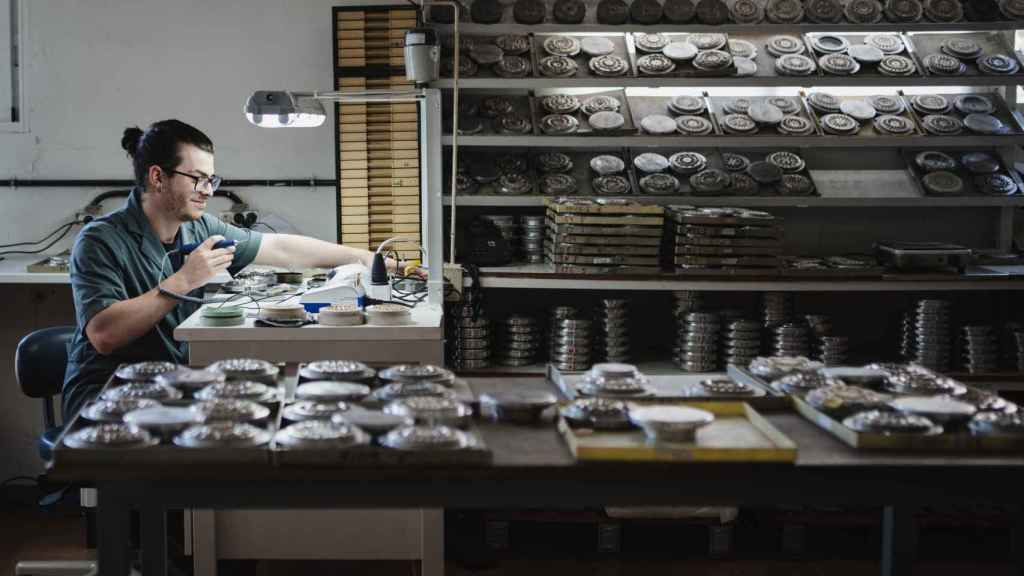
Un operario de Unidesa-Odi prepara los moldes de níquel en los que después se polimerizarán la masa de los dientes artificiales. E. E.
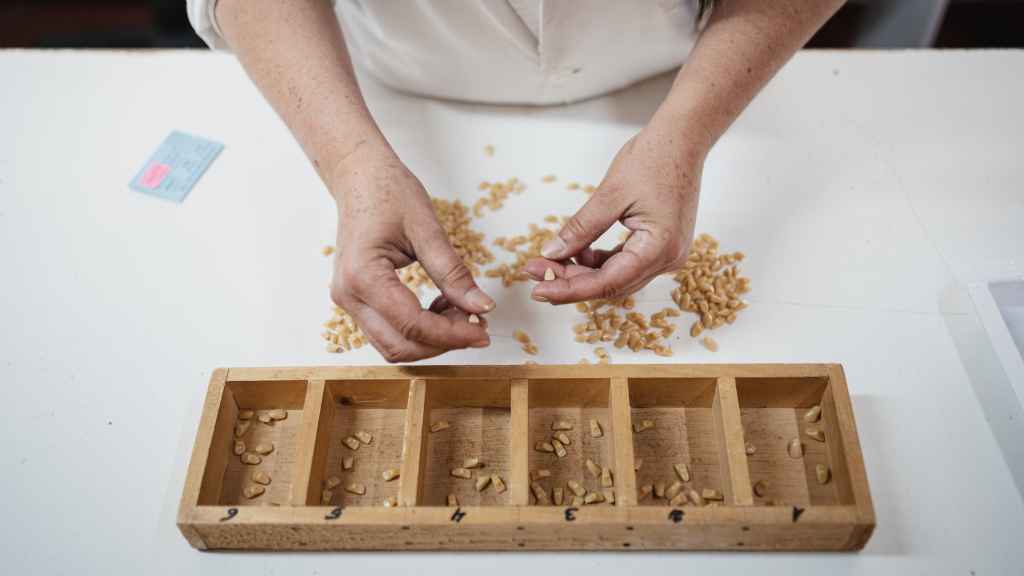
Una mujer separa varios dientes según su tipología; estos después serán pegados en una línea de cera en una tablilla. E. E.
Los Domínguez suman 60 trabajadores y más de 5.000 metros cuadrados de instalaciones diseñadas por ellos mismos y perfeccionadas "en base al ensayo y error", además de varios laboratorios y salas mecanizadas. Con estos ingredientes elaboran 12 millones de dientes cada año que destinan tanto al mercado español como a otros 63 países del mundo.
"Tras medio siglo de negocio, podemos decir que somos los únicos en España. El 70% de nuestra venta va destinada a Europa y Asia. El otro 30% de la exportación es para Estados Unidos. En el mercado nacional tenemos sólo un 16%, porque hay muchos importadores de fuera que nos hacen competencia", asegura José Domínguez en conversación con EL ESPAÑOL | Porfolio.
Unión Dental fabrica, pero no distribuye. Vende directamente a 'depósitos dentales', una serie de tiendas que proveen de material a los dentistas o laboratorios de prótesis. "Tú vas al dentista, ellos te toman la medida y se la mandan al protésico correspondiente", explica el CEO. Son ellos los que eligen el modelo y quienes, a su vez, le piden el material a los depósitos dentales, a los que previamente les ha suministrado Unidesa-Odi.
Esta mengua del mercado en favor de dientes producidos en el extranjero ha obligado a los Domínguez a diversificar su negocio. En la última década, Unidesa-Odi ha encontrado un nicho en la fabricación de los discos que después se usan como 'encías' de prótesis dentales o que son transformadas en férulas de descarga. "Hemos aumentado un 70% anual la producción de discos. En 10 años hemos crecido una barbaridad en este área. Es hacia donde realmente va a ir el mercado".
Dentro de la única fábrica de dientes de España
La fábrica del ratoncito Pérez
Domínguez guía a este diario al interior de su fábrica tembleca. En una sala de matricería hay un grupo de hombres con gafas de trabajo puliendo unos discos de níquel que hacen las veces de moldes para dientes; en otra, estos mismos discos, ya pulidos y embadurnados en cobre, se encuentran sumergidos en un baño electrolítico. Se mueven de izquierda a derecha con un sistema de bandeo lateral desarrollado por los propios ingenieros de Unión Dental. "El movimiento continuo evita que se creen bolsitas de aire", explica Domínguez. "Las piezas deben reposar aquí dentro 21 días".
Quizás estos datos puedan sonar baladíes, pero sorprende el nivel de perfeccionamiento que los Domínguez han imprimido en cada parte de la elaboración. El director general abre ahora las puertas de un almacén donde se encuentran, en bidones de un metro de altura, los polvos de resina pigmentados con los que después se elaboran las tres capas –esmalte, dentina y cuello– que lleva cada diente artificial. Enfrente hay un grupo de hombres, todos ellos jóvenes, que preparan cuidadosamente, con unas cucharas de plástico, los pigmentos que después mezclan para lograr los colores elegidos. Hay una gama de hasta 60 tipos de blanco que se adaptan a cada pieza.
"Las resinas naturales de metacrilato de metilo de las que se hacen las dentaduras después se mezclan con un líquido especial y eso da lugar a una masa termopolimerizable", instruye Domínguez, que coge con la mano un disco congelado de textura pastosa, como una esponja con forma de galleta. En el siguiente proceso, la oblea se deposita sobre uno de los moldes de níquel anteriormente descritos, los cuales se colocan en una cinta mecánica provista de un sistema de prensado. Dependiendo del tipo de diente, se colocan dos o tres capas de material –de nuevo, el esmalte, la dentina y el cuello, cada uno con su oblea– y son sometidos a un proceso de polimerización que combina las altas temperaturas con el frío, algo similar a la elaboración de las navajas de Taramundi.
Una vez acabado este proceso, los dientes ya están hechos, pero queda pulirlos, quitarles la rebaba y comprobar que todos cumplen con los máximos estándares de calidad. Después, se llevan a otra sala, aún más grande, en la que un grupo de mujeres, auténticas artesanas de otra época, los revisan y separan según su tipología –los incisivos laterales superiores por un lado, los segundos molares inferiores por otro– y los colocan en cajitas de madera o de plástico numeradas. "Estas de ahí van dirigidas a un gran cliente de Singapur". Señala unos bloques de cajas gigantes.
El último proceso antes de empaquetar los pedidos consiste en colocar, sobre una lámina de cera roja –"es para compararla con el color de las encías, aunque también las hay grises para engañar a la vista"–, los grupos de dientes. Estas están pegadas sobre unas tablillas, similares a los test PCR, en cada una de las cuales se colocan tiras de seis ejemplares de dientes. Así es como las reciben los depósitos dentales y, a la postre, los dentistas que después las colocan en nuestras bocas.
"Fíjate en la cantidad de pequeños matices que hay", dice Domínguez mientras coge dos tablillas y las compara entre sí. "Si tienes 60 años y te pones un diente completamente blanco, muy natural no queda. Hay veces que es mejor elegir uno un poco más amarillo. Después, hay dientes más baratos y más caros. La calidad es la misma, pero nosotros tenemos una gama de dientes que son más económicos porque sólo tienen dos capas de material en vez de tres, es decir, el esmalte, el cuello y la dentina. Si te fijas, en estos el cuello siempre es un poco más oscuro, mientras que en estos otros les hemos eliminado esa capa y sólo tienen dos colores".
Preguntado por hasta qué punto este tipo de productos son verdaderamente tan caros de producir como para luego tener esos precios desorbitados en las clínicas dentales, Domínguez asegura que muchas veces los precios están muy inflados. "Hay empresas que importan de Alemania por 50 € la tablilla. Nosotros, que tenemos mejor calidad que ellos, podemos vender un set de seis piezas por 12 € a un depósito dental y por 30 € a un laboratorio. Pero ya sabes que existe la manía de añadirle un cero a todo. Los dientes se pagan caros, pero lo que se paga es el conocimiento del dentista, no porque el material sea costoso. De hecho, aquí somos como los de las naranjas: cada vez tenemos menos márgenes".
También es fundamental destacar que no todos los dientes son iguales. Los más comunes, explica José Domínguez, son los de acrílico que ellos fabrican, aunque también los hay de porcelana, que son mucho más blancos y duros. "La porcelana da más sensación de viveza, pero al ser tan dura hace que los dientes naturales se desgasten antes. El acrílico, a pesar de ser un tipo de plástico, funcionalmente es mejor, porque es el más parecido en dureza a nuestra dentadura real. Dependiendo de las razas también varían los colores. No es lo mismo un negro que un asiático. Para Estados Unidos, por ejemplo, se usa una guía de colores distinta de la europea. Cada continente difiere".
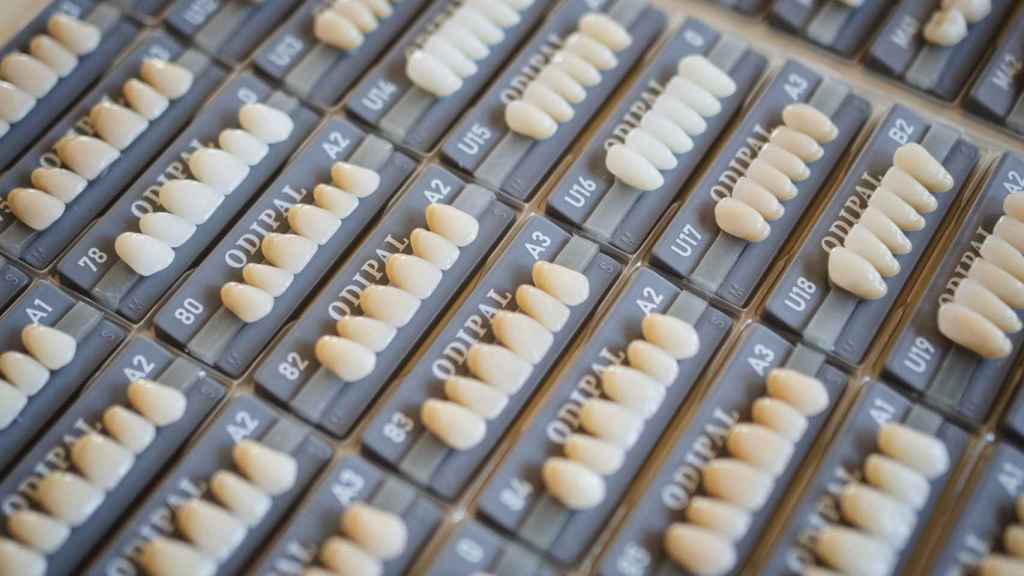
Una selección de tablillas de seis dientes de diferentes tamaños y pigmentaciones. E. E.
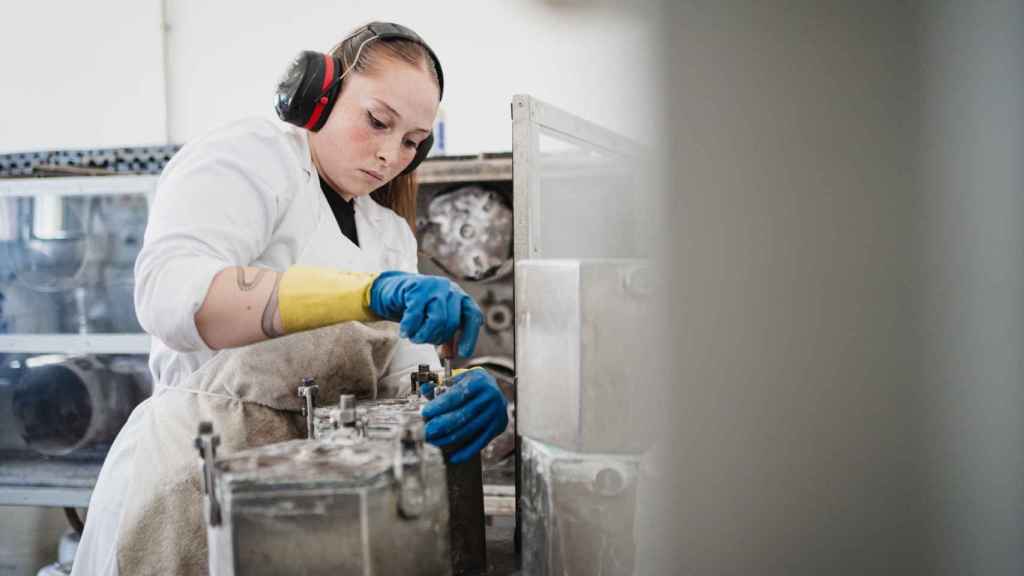
Una operaria prepara el lavado y pulido de unos dientes recién polimerizados. E. E.
PREGUNTA.– ¿Qué país tiene los dientes más grandes?
RESPUESTA.– Cada continente es distinto. Los dientes más grandes, no obstante, los tienen los del norte de Europa. También en África. Es una cuestión biológica. Después hay diferencias dentro de los propios mercados: los americanos buscan un diente muy duro que tiene unas muescas en el interior. No es la forma natural del diente, pero se parecen a los de madera que se hacían desde tiempos de George Washington. No son naturales, pero es a lo que están acostumbrados. El mercado europeo busca un modelo más blando para que se desgaste y haya que cambiarlo antes.
P.– ¿Juegan en un mercado muy competitivo?
R.– Mucho. Hay 7 u 8 empresas como la nuestra en todo Europa. Después están los chinos, que exportan mucho. Nosotros, por una cuestión de precio, estamos más centrados en Europa y Estados Unidos, aunque tenemos ocho marcas, cada una destinada a un tipo de cliente. Marruecos, por ejemplo, vende nuestro diente más barato como el top suyo, porque por debajo de eso no hay nada mejor en su país. Después, en el caso de la UE, solemos tener uno o dos distribuidores por país o importadores directos que pueden ser los propios depósitos dentales. Desde que mi abuelo montó la empresa, Alemania ha sido el más importante, mucho más que España.
[Las Últimas Cigarreras de España: Ellas Fabricaban el Tabaco pero Tenían Prohibido Fumar]
P.– ¿Y el nivel de facturación?
R.– Facturamos unos 3 millones de euros al año. No es un negocio que dé mucho dinero. A medida que los países y las personas van evolucionando, tienen mucho más cuidado con la higiene dental. Antiguamente, ibas al dentista y te sacaba el diente del tirón. Ahora, para que te extraigan una muela, tiene que estar reventada. Este negocio tenderá a desaparecer. El futuro está en los discos de prótesis dentales y en las ortodoncias.
Precisamente Domínguez finaliza el tour de su fábrica en una salita mecanizada adyacente a la habitación en la que las mujeres separan los dientes. "Ellas tienen mucho más ojo y paciencia que los hombres, por eso hay tantas", asegura Domínguez, en tono confesional, al preguntarle por el género de la mayor parte de su mano de obra. En esta nueva estancia también hay varias jóvenes que analizan, con un sistema de tomografía, si una serie de discos-obleas similares a las de los dientes contienen imperfecciones en su interior.
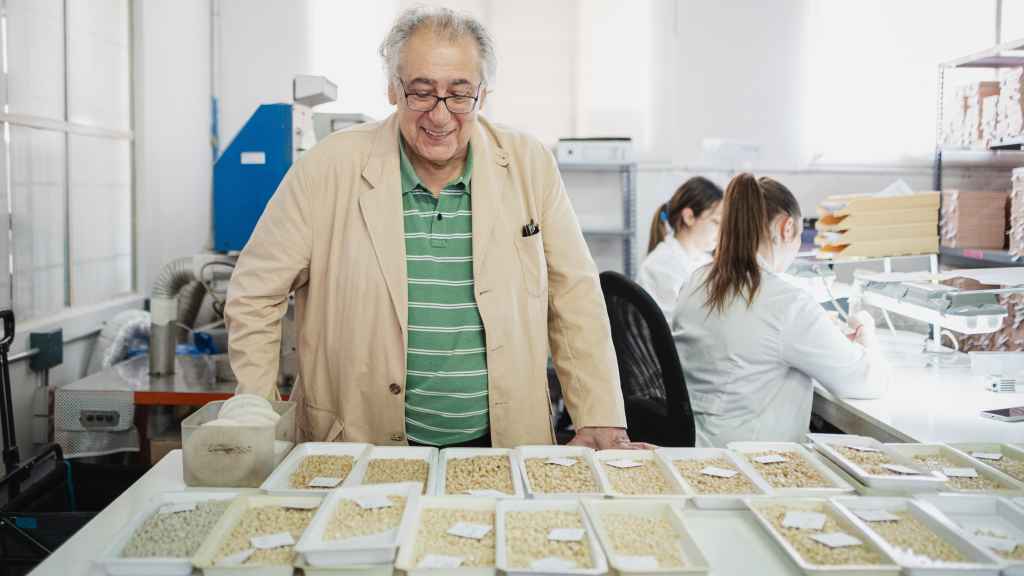
José Domínguez frente a varias bandejas repletas de dientes con diferentes pigmentaciones. E. E.

Una caja con varios dientes ya separados por colores. E. E.
"El departamento de discos es parecido: hay un equipo de preparación de masas, otro de fabricación de discos, el del repasado de los mismos y, después, hacemos la comprobación disco a disco, para ver que no tengan poros internos. Eso nos da una calidad importante en comparación con la competencia. Lo de los dientes cada vez va a menos, así que hemos tenido que reinventarnos", asegura mientras señala una gigantesca máquina en la que se fabrican cientos de discos de prótesis dentales, las encías que después lucirán en las sonrisas de los cientos de miles clientes que llevarán sus dentaduras.