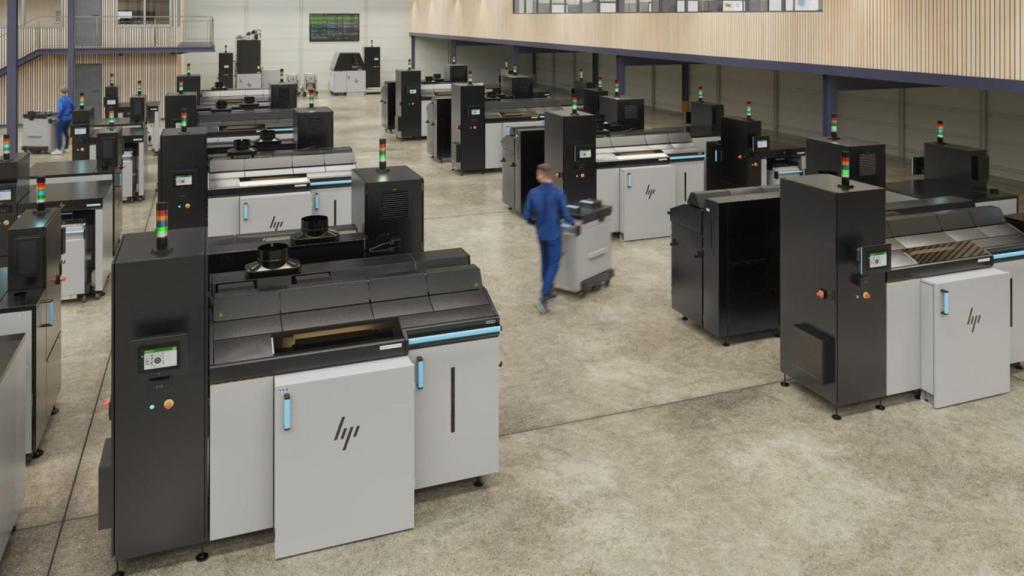
Las impresoras que crean piezas de metal en 3D. Omicrono
La impresora 3D española para crear piezas de metal a medida: de palos de golf a instrumental médico
La HP Metal Jet S100 permite la impresión digital a gran escala de piezas metálicas para los sectores médicos, industrial y de bienes de consumo.
26 octubre, 2022 02:14Las impresoras 3D han evolucionado en los últimos años, convirtiéndose en unas herramientas muy prácticas en el mundo de la industria. Unos dispositivos que por lo general utilizan un filamento de material termoplástico para crear diferentes objetos, como muñecos personalizados. Pero en España se está dando un paso más y ya se utiliza barro para imprimir una casa; y ahora una nueva solución española permite crear piezas metálicas en 3D.
[La impresora 3D que permitirá fabricar satélites enteros y piezas de naves en el espacio]
HP ha creado una impresora 3D, denominada HP Metal Jet S100, que permite la impresión digital a gran escala de piezas metálicas de alta calidad que aceleran tanto el diseño como la producción en masa de productos para sectores como el médico, industrial, de bienes de consumo y automoción. Una solución que promete revolucionar la fabricación tradicional y que se ha creado íntegramente en la sede mundial del negocio 3D de la compañía, situada en Sant Cugat del Vallès (Barcelona), donde trabajan más de 700 ingenieros y profesionales de todo el mundo.
"La gran idea detrás del 3D es poder producir en el lugar en el que necesitas el producto. La impresión 3D en plástico te da una pieza final en sólo un paso, nuestra tecnología, al utilizar metal, necesita dos o tres pasos metalúrgicos para llegar a esta pieza, por eso la impresora va acompañada por diferentes periféricos; pero como resultado se obtienen piezas más ligeras y mucho más eficientes", explica Ramón Pastor, director del centro de I+D de HP en Barcelona y responsable del negocio de 3D Metales, a EL ESPAÑOL - Omicrono.
Con polvo metálico
La compañía asegura que la mejora de la productividad, el bajo coste de las piezas y la alta calidad de las mismas son las principales ventajas de su nueva impresora. Un dispositivo que "ofrece oportunidades de producción de metales en masa para aún más partners y clientes de todo el mundo". Pero ¿en qué consiste realmente esta solución?
Pastor explica que su tecnología parte del polvo de metal y que por ahora "estamos empezando haciendo acero inoxidable, pero se puede hacer cobre, bronce y otras aleaciones". En total hay cuatro estaciones principales de hardware: una para gestionar el polvo, la impresora, una estación de curado y otra de eliminación de polvo. Además, la solución también incluye un depósito de polvo transportable.
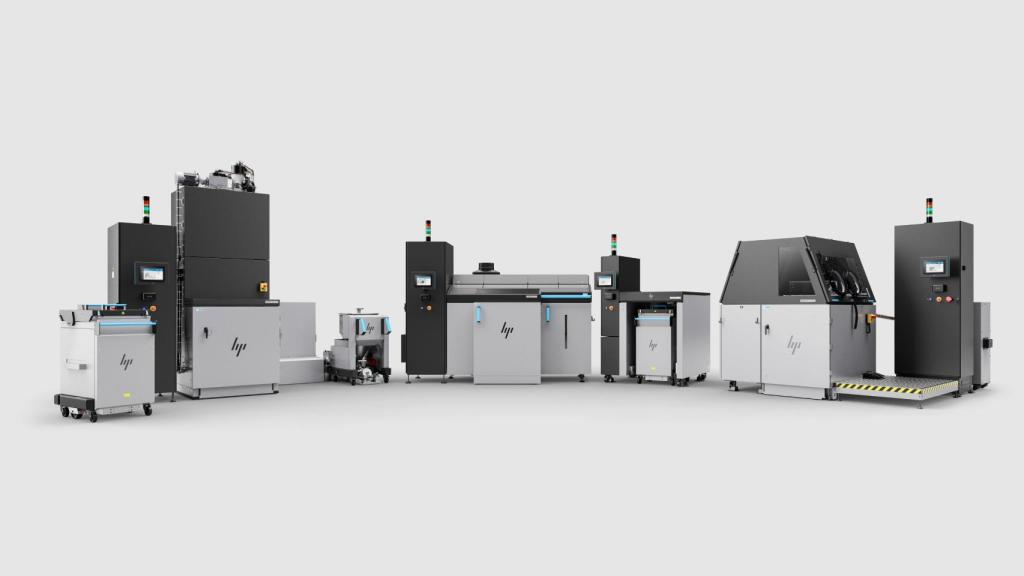
La impresora y el resto de dispositivos. Omicrono
El proceso de impresión comienza con el software, un programa que permite darle a la pieza la forma que se quiera. Tas ello "se prepara el polvo metálico, poniendo una pequeña capa en la máquina de 3D, de aproximadamente 50 micras. Con un cabezal de inyección de tinta se añade un agente aglutinador, que actúa como un pegamento, para construir capa por capa y definir la geometría deseada. Al final se obtiene una pieza intermedia que está como pegada, pero no fundida, y que se denomina 'pieza verde'", apunta Ramón Pastor.
La impresora cuenta con la capacidad de mezclar y tamizar el polvo metálico. Una vez formada la pieza, "arranca el proceso de curación. El lecho de polvo con las piezas impresas se calienta a una determinada temperatura y presión para completar la evaporación de los componentes líquidos y curar los polímeros de los agentes aglutinantes para conseguir piezas verdes de alta resistencia". Cuando es lo suficientemente denso, se lleva a otro dispositivo para la retirada del polvo.
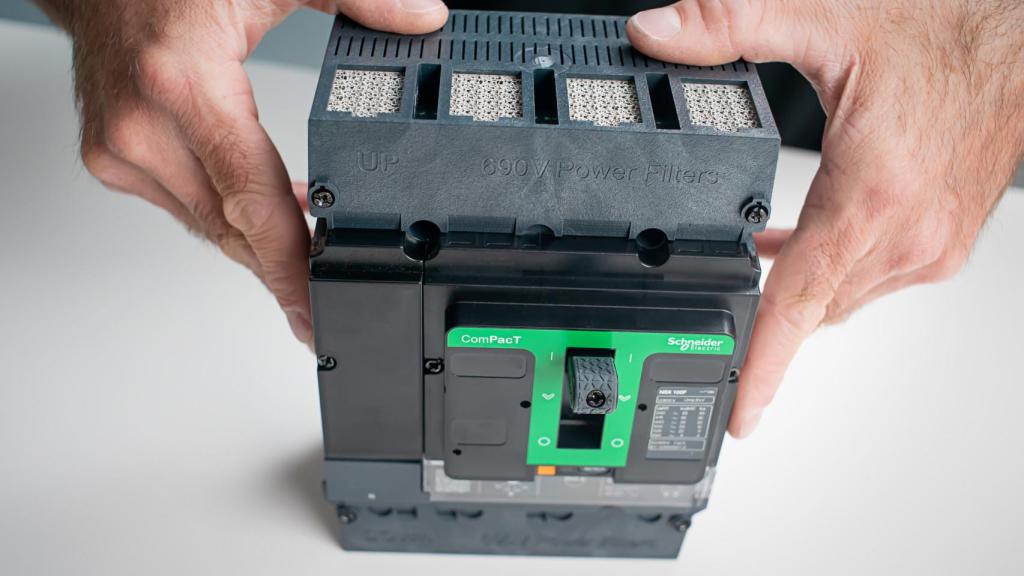
Una cubeta con el polvo metálico. Omicrono
"El equipo que quita el polvo lo que hace es dejarte con esta pieza intermedia que tiene un 50% de densidad. Para conseguir llegar al 91% o 100% de densidad que requiere la pieza, hay que meterla durante horas en un horno de sinterizado estándar que la lleva a unos 1.000 - 1.200 grados. Y ahí es cuando se obtiene la pieza final", detalla el directivo.
Una de las grandes ventajas de esta estación es que todo el polvo que se ha retirado "se puede volver a reciclar para una reutilización del 100%. Es economía 100% circular, aquí no se pierde nada". La nueva impresora de HP solamente imprime metal, "en un rango muy amplio de metales", y Pastor asegura que es sencilla de utilizar "y muy segura. No se necesita llevar ninguna protección. Al trabajar con polvo, tanto en plásticos como en metales, solamente tiene que estar en un entorno industrial".
¿Para qué se usa?
La impresión 3D de metal cuenta con una variedad de aplicaciones, aunque por el momento ninguna de ellas es la construcción. "La razón es sencilla. Nuestra tecnología tiene un límite de tamaño. Estamos hablando de piezas de hasta siete kilogramos de peso y para el sector de la construcción necesitaríamos tamaños mucho más grande. Y ahora no tiene sentido usar impresión 3D en metal para hacer cosas que midan metros", detalla Ramón Pastor.
Esta tecnología sí promete revolucionar algunas industrias, como la medicina. "La impresión 3D de metal permite hacer instrumentos médicos, como las tijeras del cirujano que muchas veces se crean específicamente para su mano o que tienen una forma u otra en función del tipo de operación. Incluso se pueden fabricar guías quirúrgicas hechas para una determinada operación", señala el directivo.
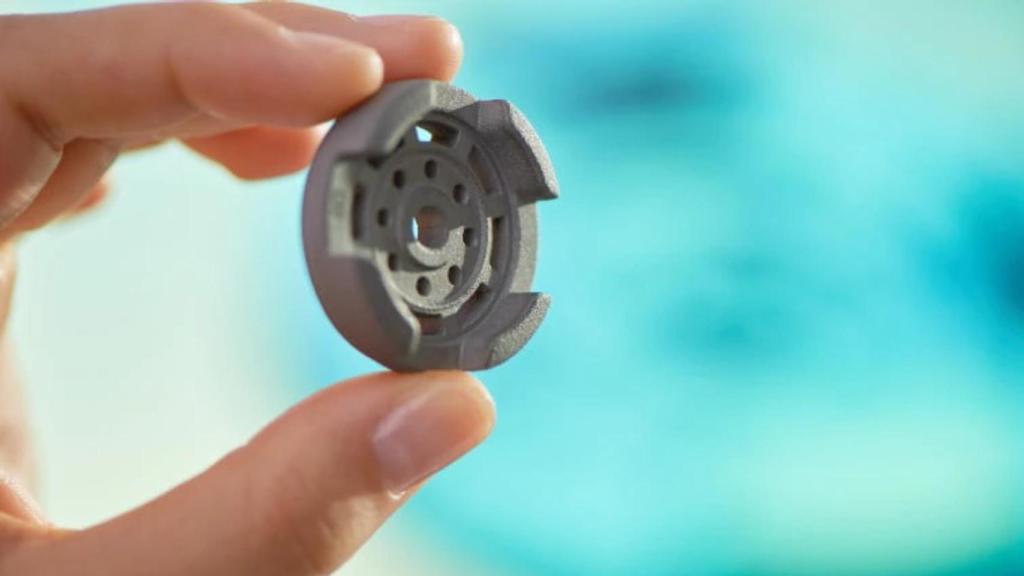
Una pieza de metal impresa en 3D. Omicrono
En cuanto al mundo de la industria, la compañía colabora con la firma Schneider Electric en la creación de "piezas metálicas para proteger al usuario si se produce un cortocircuito en un cuadro eléctrico. Un filtro que, al hacerlo en 3D, necesita un 20% menos de espacio, es más sostenible y ofrece tres veces más de vida de duración. También reduce el impacto de los gases, la presión y el calor".
En el sector de la automoción se está utilizando esta tecnología para fabricar los pilares de coches descapotables T-Roc de Volkswagen. "En bienes de consumo tenemos varios casos. Quizá el más llamativo es el de Cobra Golf, que está haciendo putters en metal 3D, concretamente la zona del palo con la que se da a la bola. Con ello consiguen tener el centro de gravedad donde se quiera y, gracias a su estructura, se logra un sonido muy gratificante cuando se golpea a la bola", explica el directivo.
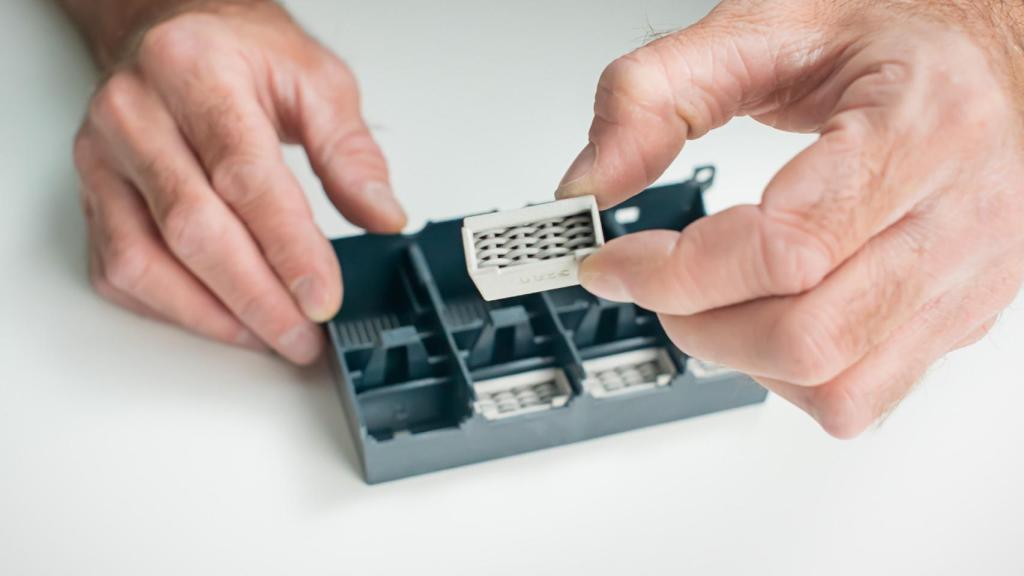
Una pieza de metal impresa en 3D. Omicrono
Esta nueva tecnología 'made in Spain' cuenta con una serie de beneficios, según sus creadores: desde crear nuevos diseños innovadores hasta mejorar la economía del cliente, "ya que los plazos del proceso de creación de las piezas se acortan y los costes debidos al trabajo manual o a los requisitos de complejidad se reducen". La impresión 3D también permite "hacer la pieza mucho más ligera y darle un diseño más eficiente y efectivo".
Otra de las grandes ventajas es que aumenta la productividad: "la inyección de aglutinante puede multiplicar por diez la productividad, ya que permite procesar capa por capa en lugar de un proceso puntual. Las propiedades isotrópicas tampoco requieren un procesamiento posterior ni la eliminación de soportes, y el uso de polvos metálicos también es más rentable que el polvo de impresión 3D basado en láser".
También te puede interesar...
- Un barrio entero impreso en 3D: casas de hasta 900 metros cuadrados y hormigón ultrarresistente
- Imprimir una presa en 3D, el próximo reto de China para la central hidráulica de Yanqdu
- Así se construye un edificio de tres plantas con una impresora 3D en sólo mes y medio
- Esta casa impresa en 3D será el lugar de entrenamiento de quienes quieran vivir en Marte